The
manual plant for ETP generally consist of :-
Collection
Tanks :
The
tanks are mostly in pits, with Acid/Alkali
resistant paint or bricks lining, to store
rinse water in segregation of v Alkali
v Cyanide v Acids v hexavalent Chrome v others individually or in permissible
combination. Each tank is fitted with discharge
pump, control panel with level control alarms,
iron grating and fittings.
Dosing
Tanks: 5
PP Dosing Tanks with fittings of suitable capacity for storage and
dosing of reagents for treatment of effluents, for gravitational
discharge, provide easy access to the tank during working &
refilling of reagents.
Treatment
Tanks:
Two Nos. PP tanks of suitable volume fitted
with motorized stirrer and compressed air
supply to ensure a total mix up of reagents,
suitable pumps. The treatment is controlled
and monitored by digital ORP and pH meters.
Settlement
Tank:
One No. Sludge settlement tank PP/PVC lined in M.S. of suitable
volume, with conical bottom, discharge valves for water and sludge,
level indicator. Such treated water is either reused or discharged
into sewer lines.
Filter
Press:
Filter Press generally manually operated of suitable capacity, with
screw pump for dewatering up to 75 %, having PP filter plates of 355 x
355 mm. to 1200 x 1200 mm. in different filtering area and discharge
ranges.
Chemicals:
Conventional chemicals for Hexavalent Chrome Reduction and Cyanide
Oxidisation are available. Some of the known neutralizing agents are
Lime, Soda Ash, Caustic, Calcium Chloride, Potash Alum, Sodium Meta
bi-sulphate and Magnesium Hydroxide. Selection should be based upon
cost, usage requirement, handling and sludge production.
Analysis
Kit:
A
ready kit of glasswares and chemical reagents
are available for easy estimation of total
cyanide and total hexavalent chromium present
in the effluent and also to test the treated
water to the discharge standards.
KCPL is the reliable source not only for complete
ETP Equipments but from pH Adjust or Neutralisation
Systems and Batch Treatment Systems, large
or small, to flow through Continuous Sedimentation
Systems, Clarifiers, Oil Skimmers, Evaporators,
Filter Presses and Sludge Management equipment.
Also, Rinse Water-Recycling Systems.
KCPLs Effluent Treatment
Systems are fully integrated, stand-alone,
equipment systems that effectively treat
process wastewater streams to comply with
local standards for discharge. Whether the
requirements are to correct pH, to precipitate
heavy metals, to remove oils from process
tanks or waste streams, to filter sediments
and particulate, to evaporate with zero
discharge, or to close-loop and recycle,
we have the exact treatment technology to
meet the need.
Komals Cyanide Destruct
Systems safely breakdown harmful cyanides
from waste streams.
FILTER
PRESSES
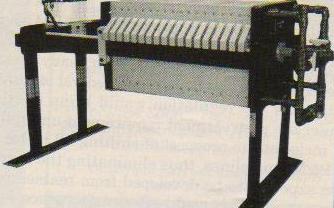
The Filter
Press has been the focus product of Komal
for many years. We have built a solid reputation
for supplying quality Filter Presses, Clarifiers,
Sludge Dryers, Complete Waste Treatment
Systems, Filter Cloths and Filter Plates.
Our Filter Presses have been used in number
of industries from plating and metal finishing.
Komal Filter Presses feature heavy duty
steel construction with polypro gasketed
plates. These filter presses can be manufactured
with manual or with a hydraulic cylinder,
high pressure closing. Komals Filter Presses
are always expandable for larger future
capacity by adding longer sidebars and additional
plates.
The filter press is
most often used in the dewatering of metal
finishing sludges. It is simple to operate,
and produces a dry, easily disposable filter
cake. Sludge from the thickener or directly
from the bottom of the clarifier, is usually
pumped via an air diaphragm pump to the
filter press. The PP filter media retains
the solid while the liquid portion or filtrate
flows through the media and discharges.
Filtrate usually returns to the collection/equalization
tank for retreatment. After a certain length
of time (2-4hours) the chambers of the press
are completely full and a filter cake of
25-35% solids has formed. The hydraulic
pressure that had been holding the plates
is now released and the filter cake is discharged
Standard
Filter Press Features
Air Driven Hydraulic Closing Pump with
Pressure Gauge on Automatic Units
Heavy Duty Hydraulic Cylinder for opening
and closing of Press.
Polypro Gasketed Recessed Plates for leak
free operation
Air Blown Manifold Piping for Air Drying
Filter Cakes.
Air Line Filter, Oiler, Regulator, and
Guage on Automatic Units.
Optional Features
Sludge Dump Carts for Sludge collection
and dumping
Cat-Walk Platform with raised legs for
disposal into Drums or our Sludge Dryer.
Automatic Plate shifter for ease of cleaning.
Distance piece for future expansion.
Leg mounted Control Panel.
Diaphragm pump for solids feed to the
Filter Press.
Filter
Press applications
Dewatering industrial Sludge
Reclaiming precious Metals
Product Filtration
Dewatering Hazardous Wastes
Process Waste Waters as per PCB approved
Treatment Systems.
CLARIFIERS
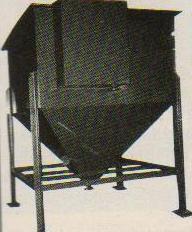
The inclined parallel plate design, manufactured
by KCPL are used as part of a ETP system
for efficient solid settlings, are constructed
of carbon steel with coal tar epoxy lining
on the inside, and epoxy coating on the
exterior. The internal plate pack is set
at 60% for optimum settling and is constructed
of a epoxy coated steel shell or with FRP
plastic plates.
The Komal Clarifiers
use the time proven concept of inclined
plate clarification. This type of clarifier
uses gravity in conjunction with the projected
settling area of the 60 degree angle parallel
plates to settle solids from the pre-treated
liquid flow. This treated liquid flows first
to the flocculation tank where polymer is
added to promote floc growth, then up through
the plate pack(s) while the solids settle
out to the bottom sludge cones. The clean
water flows out through our special laundering
troughs to plant discharge or for polishing
for water reuse. The solids are intermittently
taken from the bottom cone to a filter press
for further dewatering.
|